Hoch digitalisierte Fertigungsanlagen bieten immer mehr Sensoren und Schnittstellen, an denen wertvolle Daten abgegriffen werden können. Was aber bislang fehlte, war eine einheitliche, übergeordnete Plattform, auf der die Daten eines heterogenen Maschinenparks automatisch zur integrierten Nutzung und Auswertung zusammengeführt werden. Wo alle Maschinen in einer Sprache mit dem Benutzer und den verbundenen Softwaresystemen reden.
Die Herausforderung besteht darin, in einer bunt gemixten Fertigungsumgebung unterschiedliche Maschinen auszulesen, modernste hoch digitalisierte Anlagen ebenso wie ältere Maschinen mit niedrigerem Digitalisierungsgrad.
Genau dafür gibt es A+W IoT Smart Trace. Dieses System ist die intelligente Plattform, an die jeder Maschinenpark über Konnektoren angedockt, ausgelesen, mit Metadaten (wann, wo, durch wen unter welchen Rahmenbedingungen erzeugt und versendet) angereichert und ausgewertet wird. Mit A+W IoT Smart Trace können Glasveredler die Produktion einer einzelnen Scheibe, eines Auftrags oder einer ganzen Charge lückenlos speichern, dokumentieren und auswerten.
Das System stellt den Benutzern alle benötigten Informationen per Mausklick zur Verfügung.
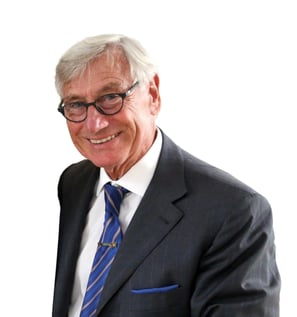
Günter Weidemann, Gründer und Inhaber der Schollglas-Gruppe: „Wir setzen auf durchgängige Digitalisierung und schaffen bei Schollglas Sachsen eine Industrie 4.0 Umgebung, die bislang in der Glasindustrie einmalig ist.“
Schollglas Sachsen: Datenerfasssung und -Auswertung automatisieren
Die Firma Schollglas Sachsen könnte man als den „Projektgeschäft-Standort“ unter den 13 Schollglas- Niederlassungen bezeichnen. Dahinter verbirgt sich ein hoch leistungsfähiger Vollsortimenter, der Spitzenprodukte europaweit, im Projektgeschäft auch weltweit vertreibt. Das Unternehmen verfügt über alle technischen Voraussetzungen und das Know-how, auch anspruchsvollste Objekte durchgängig abzuwickeln. Auf 30.000 m² Produktionsfläche fertigen 400 Mitarbeiter aus 120 -Glasarten sämtliche Architektur- und hoch spezialisierte Fahrzeuggläser, vor allem das gesamte Spektrum der technischen- und Sicherheitsgläser sowie Performance-Isoliergläser bis zu Bandmaßgröße.
Schollglas zeigt hier seine Innovationskraft: So wird mit Hilfe einer speziellen Laseranlage GEWE®-com connect gefertigt, eine moderne Verglasungs-Lösung für Gebäude und Züge, die den direkten Durchgang von Mobilfunksignalen durch die Scheiben von Gebäuden und Eisenbahnzügen ermöglicht – das kann nicht jeder Glasveredler anbieten.
Modernste Schleif- und Drucktechnik ermöglicht kreative Lösungen, die beste Performance mit elegantem Design vereinen und so Wege zu faszinierender Architektur und atemberaubender Fassadengestaltung eröffnen. Gemeinsam mit Partnern, oft Metallbau-Unternehmen, entstehen Vorzeigeprojekte, die zu den weltbesten gehören und bis an die Grenzen des technisch Machbaren gehen. Schollglas-IT-Leiter Torsten Brose: „Es gibt praktisch kein Flachglas, das wir hier nicht fertigen können.“
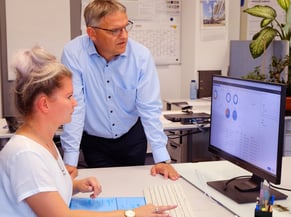
Am Dashboard stellt die Mitarbeiterin Auswertungen nach den gewünschten Kriterien zu aussagefähigen Diagrammen zusammen: Ein Blick in den Datencontainer von A+W IoT Smart Trace.
Wer sich in solchen Sphären bewegt und nicht selten große Mengen an Scheiben rund um den Globus liefert, benötigt eine durchgängige und sichere Fertigungsdokumentation, von der Einzelscheibe bis zur kompletten Charge. Zuverlässige Qualitätssicherung ist essenziell. Freilich macht Schollglas Sachsen das auch jetzt schon, aber mit umständlichen, manuellen Verfahren, bei denen schon ein Schreibfehler oder Zahlendreher zu falschen Zuordnungen und damit erschwerter Verfolgung führen kann. Beim Häuslebauer lässt sich das sicher irgendwie lösen, aber bei Mammutprojekten mit hunderten von Scheiben oder mehr? Bei einer Reklamation kann die Informationssuche aus diversen Ablagen Stunden wenn nicht Tage an Aufwand erzeugen. Mit A+W IoT Smart Trace sind diese Daten nun jederzeit per Mausklick verfügbar.
Das Pionierprojekt: Produktionsdaten digital managen
Es empfiehlt sich, derart anspruchsvolle Digitalisierungsprojekte wie A+W IoT Smart Trace nicht gleich mit allen Technologien umzusetzen – vor allem, wenn man der erste Anwender überhaupt ist. Prozesse müssen neu definiert, Mitarbeiter einbezogen und geschult werden. Zwar drohen keine Katastrophen wie Maschinensillstände, entgangene Aufträge etc., aber komplexe Projekte wie ein IoT-Datenerfassungs- und Verwaltungssystem lassen sich besser umsichtig und Step by Step aufbauen. Denn am Ende soll ja ein intelligenter Datencontainer zur Verfügung stehen, der nicht nur vollständig, sondern auch leicht zugänglich ist – mit ergonomischer Oberfläche und cleveren Dashboards. Das Suchen, Finden und Weiterverwerten von Daten und Dokumenten muss mit nur wenigen Mausklicks schnell und mühelos erledigt werden können.
Daher begann Schollglas Sachsen zunächst mit den Technologien Zuschnitt, Isolierglas, ESG und Heat Soak.
„IoT bietet heute unendlich viele Möglichkeiten, die nicht immer einfach zu bewerten sind. Mit einem gezielt begrenzten Projekt, welches bereits einen hohen Nutzen bietet, haben wir hier völlig neue Wege erschlossen.‘“
Dr. Klaus Mühlhans, Technical Director A+W
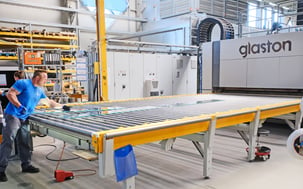
Der ESG-Ofen liefert eine Menge technischer Daten bis hin zum gescannten Bild des Ofenbettes; über den A+W IoT Smart Trace -Konnektor werden sie vom Ofen übernommen und dem Kunden als übersichtliches PDF zur Verfügung gestellt.
Jeder Scheibe ihre Charge!
Im Zuschnitt wird die Chargennummer jeder Scheibe erfasst. Was früher ‚mit Zettel und Bleistift‘ gemacht wurde, erfolgt nun über den A+W Zuschnitt-Leitrechner A+W Realtime-Optimizer.
In der Isolierglasfertigung erfassen die Mitarbeiter nur die Chargen der Versiegelungsmittel im Moment des Wechsels. Anstatt die Nummer jedes Dichtstoff-Gebindes manuell in Listen einzutragen, genügt heute der Scan eines Barcodes auf dem Fass - eine einfache praxisgerechte Lösung, mit der die vorher im Wareneingang zugeordnete Chargennummer voll automatisch zur A+W IoT Smart Trace Datenplattform übertragen wird. Die Zuordnung der Chargen zu den einzelnen Isolierglasscheiben erfolgt dann vollautomatisch, da das System über die Stückliste der Scheibe den aktuell verwendeten Dichtstoff ermitteln kann. So entsteht für die Mitarbeiter kein Mehraufwand, wenn die Dichtstoffe häufig wechseln (zu einer Zeit hat die Maschine in der Regel verschiedene Dichtstoffe im Zugriff).
So ist mit wenigen Handgriffen gewährleistet, dass wenn nötig auch noch nach Jahren die Bestandteile einer Isolierglasscheibe sicher mit Chargen verknüpft und blitzschnell per Mausklick dargestellt werden können.
Mehrwert für den Kunden: Qualitätsnachweis für jede ESG-Scheibe
Moderne ESG-Öfen erzeugen jede Menge Daten, die zur durchgängigen Qualitätskontrolle von hoher Wichtigkeit sind; man muss sie nur dem Ofen so entlocken, dass sie übersichtlich aufbereitet zur Verfügung stehen und archiviert werden können. A+W IoT Smart Trace erstellt für jede gehärtete Scheibe eine übersichtliche PDF-Liste mit allen relevanten Daten, die durch verschiedene Sensoren und Scanner-Systeme des Ofens erzeugt wurden - inklusive einer Abbildung der Ofenbettbelegung. Diese Daten werden nicht nur im Archiv abgelegt, sondern dem Kunden mit jedem Auftrag zur Verfügung gestellt.
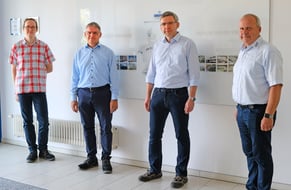
Dieses Team setzt das A+W IoT Smart Trace-Projekt um – von links: Robert Titze, IT Schollglas Sachsen; Torsten Brose, ppa. Leitung IT Schollglas-Gruppe; Frank Blum, Leiter Arbeitsvorbereitung Schollglas Sachsen; Heiko Schuh, A+W Clarity Director Sales Central Europe. Nicht anwesend: Dr. Klaus Mühlhans, Technical Director A+W und Thomas Lenz, Werkstudent A+W.
Von der Erfassung zur Visualisierung
Das Ganze ist übrigens in der Fertigung wenig spektakulär anzuschauen. Es werden lediglich Barcodes an Produktionsrechnern eingegeben oder gescannt. Die Akzeptanz der Mitarbeiter ist hoch, weil sich ihre Arbeit positiv verändert – sie gewinnen ein Stück Sicherheit bei der Eingabe hinzu, der Chargen-Zuordnungsprozess erfolgt ordentlicher und systematischer.
Die Auswertung der Daten und die Verknüpfung mit dem ERP System erfolgen im kaufmännischen Bereich über intelligente Tools wie hoch ergonomische Dashboards, wo sämtliche IoT-Daten nach den Anforderungen des Benutzers als übersichtliche Diagramme visualisiert werden: Die Daten aus A+W IoT Smart Trace können direkt geladen, miteinander kombiniert und intelligent dargestellt werden.
In der Auftragsbearbeitung steht als weiteres starkes Visualisierungs-Werkzeug eine Sidebar zur Verfügung, in der sämtliche zum Auftrag gehörigen Daten interaktiv dargestellt werden. Der ERP-Sachbearbeiter sieht alle Details, die über A+W IoT Smart Trace erfasst und in den Datenspeicher gesendet wurden, wie etwa Chargennummern, das am Ofen erzeugte PDF mit sämtlichen Vorspann-Daten, die Chargennummern des TPS-Materials von der Iso-Linie und das Heat Soak-Protokoll.
Digitalisierung als Kundenservice
Mit den vier Pioniertechnologien ist das Projekt noch in der Anfangsphase, doch Torsten Brose, IT-Leiter der Schollglas-Gruppe, ist begeistert und sieht schon jetzt viele Vorteile:
„Wir haben schon mehrere Softwarelösungen gemeinsam mit A+W pilotiert und befinden uns auch mit A+W IoT Smart Trace auf einem guten Weg. Mit der automatischen Kopplung von Maschinen und erzeugten Daten erzielen wir höchsten Nutzen mit deutlich weniger Aufwand – das spart Zeit und Geld. In erster Linie profitieren davon unsere Kunden. Wir können nun den Qualitätsnachweis mit jedem Auftrag als zusätzlichen Service erbringen, unabhängig von eventuellen Nachfragen. Mit der Einbindung aller Maschinen in A+W IoT Smart Trace erreichen wir einen enormen Digitalisierungsgrad über sämtliche Anlagen und realisieren ein weiteres Stück Industrie 4.0.“