Have you recently taken the Voralpenexpress and traveled in one of the modern "Traverso" trains? Then perhaps you registered with satisfaction that you had outstanding online connections for your smartphone or notebook while you were traveling. This wonderful experience is possible thanks to an innovative company in the Upper Palatinate: FLACHGLAS Wernberg is one of the leading providers of highly-specialized performance and safety glass for demanding challenges, and it is the market leader in the intelligent vehicle glass sector, for example for railcars, buses, and ships.
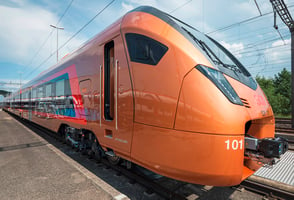
Voralpenexpress "Traverso" with FLACHGLASconnect technology
FLACHGLAS Wernberg's product range is highly complex, for it also includes the areas of facades and interior glass. With more than 600 employees, the company produces glass for ambitious glazing projects, something that only a few companies can provide in this quality, especially with the expected delivery reliability. The company's most important markets are Germany, the Benelux countries, Austria, and Switzerland.
Market leadership thanks to constant innovation
The market is changing all the time and there is increasing demand for functional glass that hardly anyone requested just a few years ago. Only extremely innovative processes and technologies make it possible to realize ever-changing fascinating ideas - that's something that the people in Wernberg understand. These include the Wernberg thermal damping, an exclusive coating process with which insulated glass weighing up to two tons can be coated; this process also enables the after-the-fact coating of glass that has already been bent.
Intensive research makes it possible for FLACHGLAS Wernberg to produce window modules for railcars that are approximately 40% lighter than most modules are currently. For an average ICE, this reduces the weight of a train by three tons and makes a significant contribution to reducing its CO2 footprint.
One of the most important current development at this glass finisher in the Upper Palatinate is FLACHGLASconnect ®, a glazing system for railcars and architectural glass that ensures perfect mobile phone reception and an excellent Internet connection without additional routers. This great function is possible thanks to a lasered pattern, the so-called 'mosquito net,' in the metallic low-e coating of insulated glass units.
Complex technologies, planning and control processes, and complex logistics are required for this. And high demands are made not just of the machine park, but also of the controlling software.
Software challenge:
Mapping everything – controlling processes
Increasing internal requirements and existing software that had been pushed to its limits caused the company to take a decisive innovative step in 2017. Since May 2017, a project team consisting of FLACHGLAS Wernberg colleagues and software experts from A+W has been working at top speed on the implementation of a continuous software solution that is fit for the future; one that is supposed to seamlessly map all corporate processes, from the office to all of production, to control of delivery processes. The FLACHGLAS Wernberg project was an enormous challenge for both partners – across Europe and probably elsewhere in the world as well, there is probably no other flat glass finisher with comparable demanding, complicated structures.
During the project, the entire organization was put on the test bench. The goal was to tighten up all flows and make all processes dynamic. FLACHGLAS Wernberg wanted to save valuable material and ensure maximum quality thanks to increased automation with less manual handling.
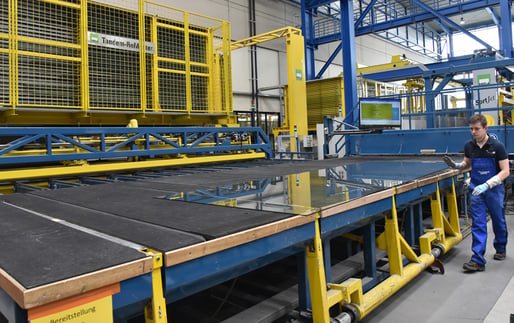
Cutting site with tandem remaster, SortJet, and A+W Production Terminal
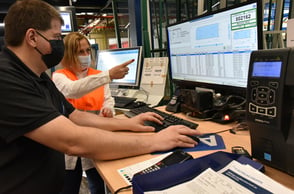
A+W Production Terminal with label printer on the Systron CNC processing system
"Open-heart surgery"
After careful process analysis and goal definition, A+W constructed a complete system environment in Wernberg. First, it functioned as a test system for the implementation of all project steps. In addition to the server environment, the heart of the new system, more than a hundred control computers and monitors and PDC scanners, ensured that information was visualized, machines controlled in real time, and process steps registered.
At the same time, all master data was examined and some of it restructured, the entire article structure was adjusted, and product names were unified. In the future, articles will be defined and entered according to the A+W BOM concept – order entry will be more secure, and the integration of technical order entry more demanding. Externally purchased services, for example, the installation of glass in insulated glass units or in frame systems for railcars, can now be integrated into the production and order process more easily ("extended workbench").
The new software system "knows" the highly complex product range of FLACHGLAS Wernberg down to the last detail – commercially and technically. It controls the entire machine environment. In close cooperation with machine manufacturers, A+W has developed the best state-of-the-art interfaces in the industry in order to make the production process faster and more secure: for every machine is only as good as the software that controls it.
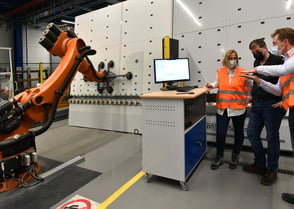
Robot loading on the Systron CNC edge processing system
As in a good marriage
Of course daily business has to continue during the entire course of the project – not least for the members of the project team. This was an operation on the company's "open heart." The members of the project team, from FLACHGLAS Wernberg and A+W, did yeoman duty and pushed their limits – and they were rewarded with a successfully completed project. The outstanding cooperation between the partners was responsible for this. Rudolf Fleischmann, team manager at IT FLACHGLAS Wernberg: "During the whole project, the teams from Wernberg and A+W worked together very well and professionally. It's kind of like in a good marriage: sometimes we quarreled, but we made up again quickly too. This way, we always advanced the project constructively and with great engagement. And the most important binding factor was trust."
Monika Schmid, A+W project manager, underscores this statement and points to the pandemic as an additional challenge: "The project was challenging both because of the complexity of the product range and due to the sheer size of the location. The business processes were simplified and made more transparent when introducing the A+W software, and the complexity of interfaces was reduced. The fact that the project goals were realized under the difficult pandemic conditions is thanks to the team's great performance. I would like to take this opportunity to thank all the participants once again."
The conversion to the new software did not cause any production shutdowns; cutting was smooth from the very beginning. However, the great complexity of the project caused some friction losses in the time after the conversion, which also affected FLACHGLAS Wernberg's delivery reliability from time to time. Today, except for a few small issues, these problems have been eliminated. In connection with the basic systems A+W Enterprise and A+W Production, a continuously networked system of control computers, control monitors, and PDC scanners ensures that information is visualized, machines ae controlled in real time, and process steps registered. Production papers are becoming obsolete. Thanks to the consistent entry of each individual lite, the employees in order processing can respond to customer inquiries reliably at any any time.
Synergies in the Flachglas Group
In addition to FLACHGLAS Wernberg, there are three other high-performance companies that are part of the Flachglas Group; they complement the manufacturing and delivery of innovative glass very well and deliver quickly and reliably within the group. A+W software is well-known to the Flachglas Group – the tempered glass specialist GLASPROFI and Flachglas Schweiz are both working successfully with it.
The new system will provide additional opportunities, but also challenges: it will no longer control individual companies, but rather, after the roll-out is complete, network the entire corporate group and ensure that structures are continuous. That's why the other locations are already considered in the system in Wernberg – a structure is being prepared, which when the expansion is complete, will ensure more reliable processes between the branch offices. Employees of GLASPROFI and Flachglas Schweiz provided critical support for the project implementation in Wernberg thanks to their longstanding experience with A+W software. With all of this, the Flachglas Group has achieved a degree of automation and digitalization that only a few glass finishers and insulated glass manufacturers around the world have achieved.
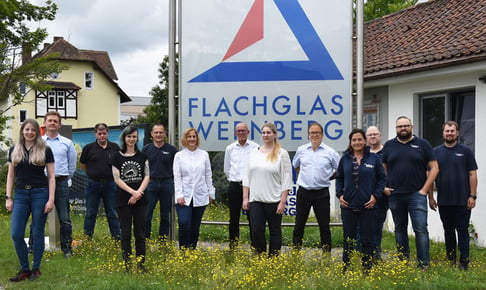
Proud of their succesful project – from L: Melanie Hollweck, FLACHGLAS Wernberg project team; Dr. Alexander Trenin, A+W sub-project manager A+W Production; Daniel Zanner, FLACHGLAS Wernberg project team; Jasmin Sorgenfrei, FLACHGLAS Wernberg Marketing; Rudolf Fleischmann, team leader at IT FLACHGLAS Wernberg; Monika Schmid, project manager A+W; Richard Gröschel, team manager Sales BHI FLACHGLAS Wernberg; Jacqueline Linsmeier, FLACHGLAS Wernberg project team; Alfred Cortisse, A+W COO EMEA/APAC; Thea Althaus, Senior Sales Manager FLACHGLAS Wernberg; Christian Igl, FLACHGLAS Wernberg project team; Florian Irlbacher, Operations Manager FLACHGLAS Wernberg; Martin Biegerl, FLACHGLAS Wernberg project team