The customer measures a supplier's quality by the quality of the company's delivery logistics. Delivery is one of the most important customer touchpoints. Timeliness, completeness, and the condition of the delivery are critical for the customer, especially if the product - as is generally the rule in the flat glass industry - will be processed further and the delivery has therefore been incorporated into the customer's production planning from an early stage. Delivery on short notice and timely construction site delivery are services that are simply expected today.
.jpg?width=305&name=GLASWELT_Logo%20(002).jpg)
That's why delivery logistics and the handling of complaints are so important for the customer. How quickly can the flat glass partner delivery the replacement lite? Can the customer adhere to his production sequence or will there be critical delivery bottlenecks with the end product? Delivery logistics begin with the supplier's production planning, whereby the delivery dates match the production sequence. In the end, the customer decides what will be produced and delivered first.
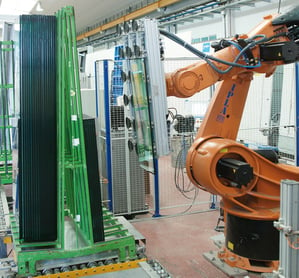
The production of complex lites and insulated glass units has to be done so that the lites are available on-time for loading on the truck on the right rack in the right sequence for the right route. This means that the racks with the lites have to be prepared and optimized for loading using a perfect shipping logistics system. Delivery and packing logistics have to work smoothly together in highly integrated fashion. Manually, this is very difficult to achieve; it is labor-intensive and expensive.
Packing logistics begins with the individual rack. In well-organized insulated glass operations, products are placed on shipping racks directly and so they are optimized. Highly specialized software systems such as the A+W Rack Optimizer ensure that the packing restrictions for the shipping rack are considered, as is the order in which the customer will remove items from it.
In the Industry 4.0 world, the racks will be loaded by robots controlled by software – precisely to the millimeter, quickly, and without manual intervention. Nothing will have to be picked or repacked; optimally loaded shipping racks are ready for packing on "their" truck.
Electronic packing information
Based on barcode registrations, precise packing lists will be created, which can be sent to customers electronically. This way, the packing information is present in the customer's IT system right away and it does not have to be placed on the shipping rack in paper form – which increases the security and availability of the information.
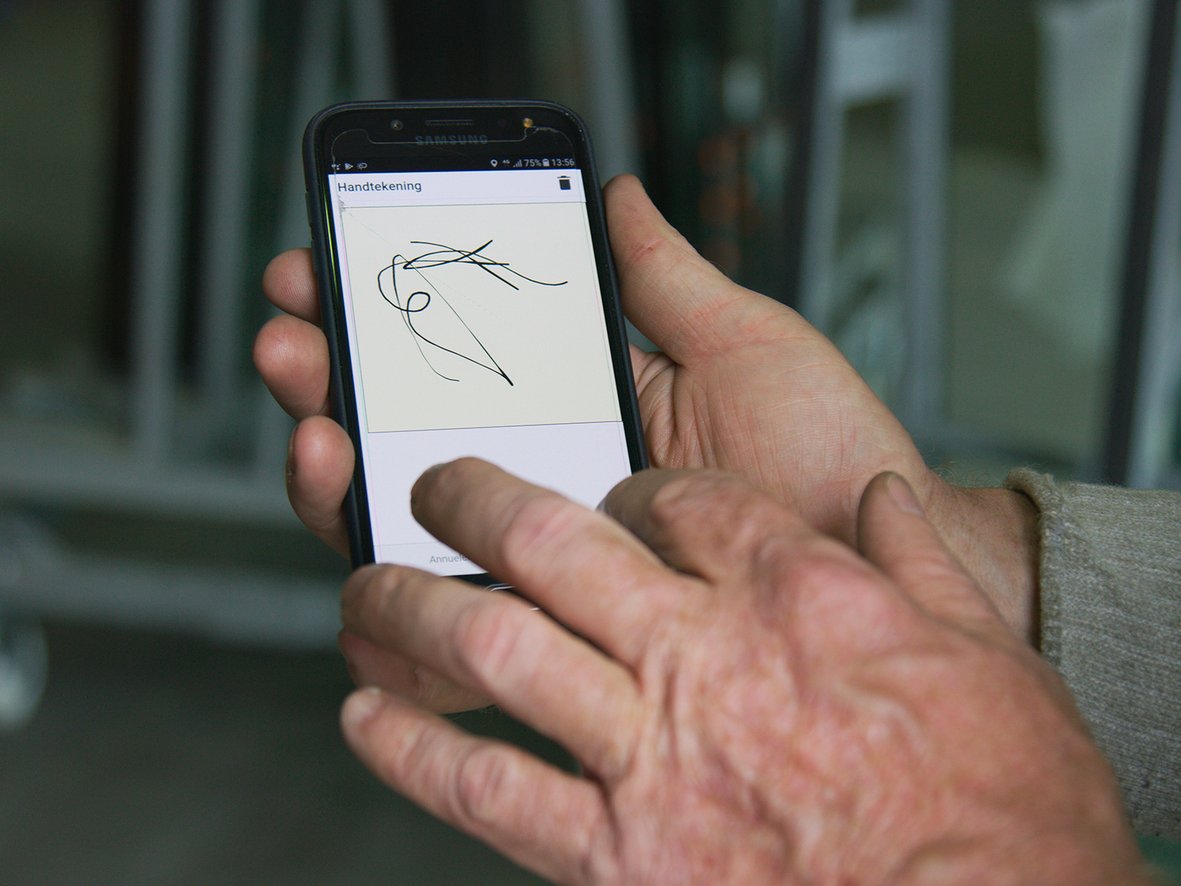
Now the customer knows exactly which lite will be delivered when on which truck and rack, and if necessary, also which broken lite must be re-delivered. Naturally the lite sequence on the shipping racks is also documented on the packing list. This is another little piece of digitalization that increases the efficiency and security of the delivery process enormously.
Load optimization
In addition to other parameters, good logistics optimizers also optimize the loading of the trucks considering various kinds of racks. For example, various A racks can be optimized together with boxes for maximum utilization of the cargo space. Here, depending on the truck type, the delivery sequence also has to be considered – it's useless if the storage space is used optimally but racks cannot be accessed easily in the delivery sequence. State-of-the-art logistics systems consider this since they examine both packing and delivery logistics.
Route planning
Before loading of the trucks is optimized, if it is configured properly, the supplier's logistics software has long since taken care of all the route planning. State-of-the-art, highly automated systems plan the shortest route automatically, considering all destinations, in order to reduce time and costs. This solution integrates entire truck fleets and route parameters and analyzes the driving times in order to guarantee that deliveries or pick-ups can be made as cost-effectively as possible within the planned time.
A+W Rack Optimizer generates sequences with which high-priority items can be delivered. Routes are adjusted to traffic in order to achieve the best results. During the route calculation, parameters such as storage space (storage meters), delivery times, hold times, and priorities selected by the user are considered.
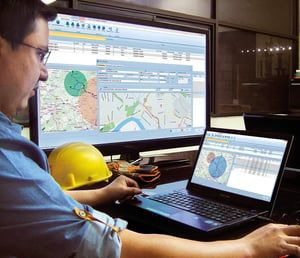
Smart Delivery: delivery in the age of Industry 4.0
Of course comprehensively digitalized systems such as the A+W Logistics Optimizer also help with delivery to the customer. This is how the driver can use a delivery app on a smartphone to book the delivery and report it back to the ERP system in real time. There, the dispatch manager can monitor the delivery of the route online and react directly to reports such as "Lite 0815 broken" and initiate re-production.
This way, the supplier frequently saves several days and in many cases can deliver the re-produced lite the very next working day. The driver also has the opportunity to photograph the delivery situation with a smartphone (where? in what condition?); the picture remains in the system and serves as additional proof of proper delivery, if necessary deviating delivery point and irregularities such as damage, etc.
Using GPS coordinates, planned and also deviating delivery points are reported and are therefore available at any time for after-the-fact evaluations.
When the customer confirms correct delivery, invoicing can be initiated immediately – and so more time and money is saved. The system also supports the delivery and pick-up of additional racks and it can thus be integrated completely into route optimization.