DYNAMIC PRODUCTION – THE BEST QUALITY
With a fascinating business model, the owner-operated company Spiegel Thomas has redefined the production and delivery of high-quality interior glass. This Munich glass processor delivers any sheet ordered anywhere in Bavaria within twenty-four hours; TG sheets within forty-eight hours.
![]() |
![]() |
Two Intermac Master Edge processing centers and several Forvet CNC drilling and milling centers complement the Chiara processing line and ensure maximum processing capacity with top quality.
High-tech production
The basis for high-quality, quick processings at Spiegel Thomas are the networked CNC processing centers. In addition to the Forvet Chiara processing line with integrated waterjet cutting, the machine park includes several Forvet CNC drilling and milling machines, as well as two Intermac Master Edge CNC processing centers. Anything that cannot be ground on the CNC machines because it's too thin is produced on two single-sided grinding machines. Around the clock, two TG furnaces ensure that there is always enough tempering capacity available.
Integrated software control
2001: Spiegel Thomas selects A+W-Software in order to increase productivity in order entry. Today, A+W software is used across the company to ensure efficient production organization. Spiegel Thomas produces almost exclusively a batch size of one. If the CNC machines had to be programmed manually for each sheet, the company would not be able to achieve its production volume: its business model would not be feasible.
With a fascinating business model, the owner-operated company Spiegel Thomas has redefined the production and delivery of high-quality interior glass. This Munich glass processor delivers any sheet ordered anywhere in Bavaria within twenty-four hours; TG sheets within forty-eight hours.
Early on, Spiegel Thomas recognized increasing customer requirements with respect to delivery, committed service, and the best quality, and the company oriented itself consistently accordingly. Sixty well-trained employees and state-of-the-art CNC machines controlled by intelligent A+W software ensure the best performance and extremely short throughput times in production. "Dynamic production and top quality," explains Managing Director Maximilian Rössler,"are only possible with a committed team and the highest degree of automation." Therefore, at Spiegel Thomas, the critical requirements for Industry 4.0 production have already been implemented.
For automatic activation of the machines, Spiegel Thomas relies on the A+W interface A+W CAM-DXF, which in addition to geometric data for the sheets also delivers machine-related information about tools, suction cup positioning, etc. The CAM-DXF files are generated in the A+W CAD Designer, a CAD system custom-tailored for flat glass. Of course sheet information provided by the customer can also be imported here and templates digitized. The transfer to the machine is done directly using the A+W Production Terminal software, which also provides visualization and sheet tracking.
Paperless and transparentYou could search in vain for production papers in production at Spiegel Thomas: the bar code label generated in work preparation includes all critical production information. The machine operator scans the sheet label at the intake of the CNC machine and then sees all technical data for the sheet on the A+W Production Monitor. This includes dimensions, processings to be done, tools, etc. If everything looks right, he initiates processing with a mouse-click. When all processings are complete, the sheet is marked "finished" in the production database with another barcode reading at the machine outlet. Thus, the new sheet status is reported to all production points, and also to the upstream A+W Business ERP system. This, in turn, creates great transparency and process reliability: no glass is lost or produced twice. In order processing, employees can provide customers with reliable information about the processing status of a sheet at any time. |
![]() |
"Finished" message for a sheet at the end of the Chiara processing line. |
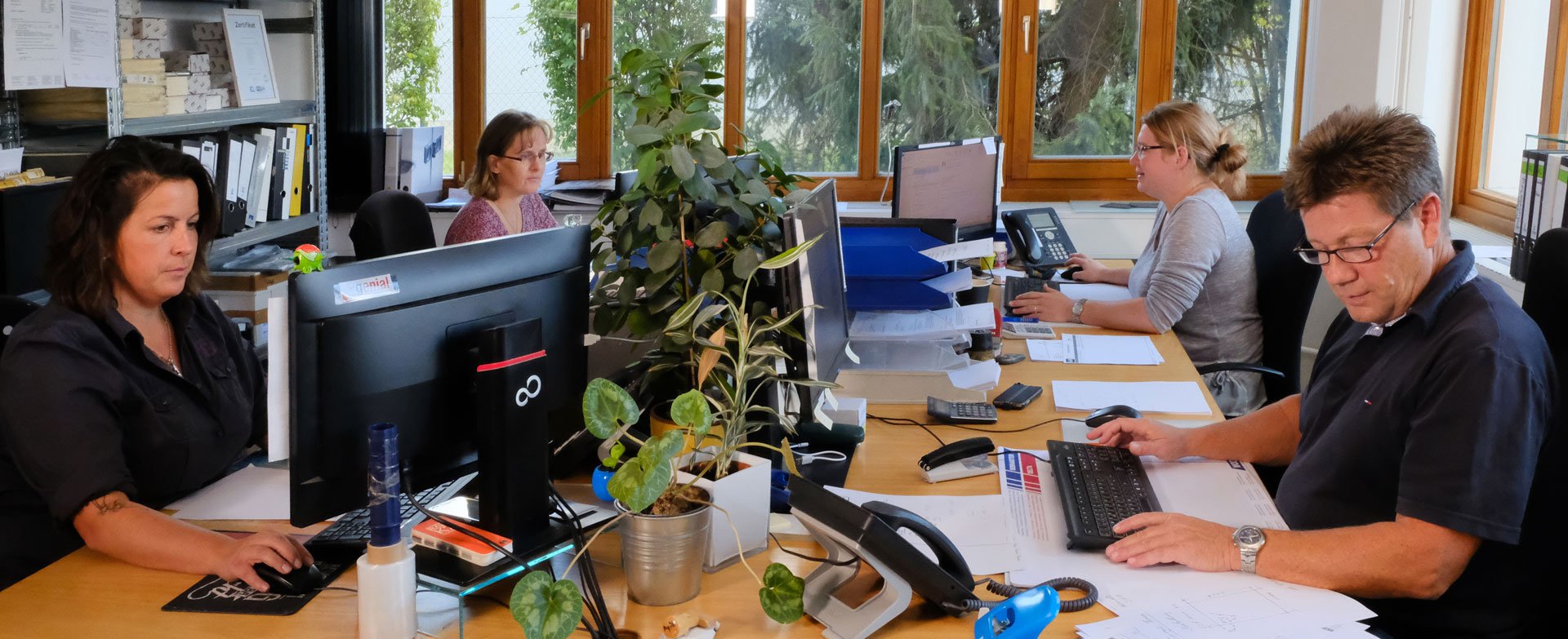